February 5, 2023
Concrete’s carbon footprint still weighs heavy – what impact can sprayed concrete processes have?
The topic of sustainability has long since moved sharply into focus for industries and societies around the world. Faced with the looming climate crisis, awareness of sustainable development has come to the fore and made its way into the underground construction industry. ‘Reduced Carbon’ is the new currency in sprayed concrete.
Underground equipment is forever evolving and technology is advancing, whether as upgrades to concrete pumping systems, additional remote-control functions, low carbon battery-powered vehicles, technologies for sprayed concrete thickness monitoring, automated concrete spraying and other techy add-ons, not to mention improvements in sprayed concrete chemical technology to support ever-increasing technical requirements. Reducing cement contents increases in usage of low-carbon binders such as ground granulated blast furnace slag, fly ash, and limestone. The key to our success is ‘design smart’ and the ability to reduce the cement and still maintain ultimate strength development so here’s my spin on it.
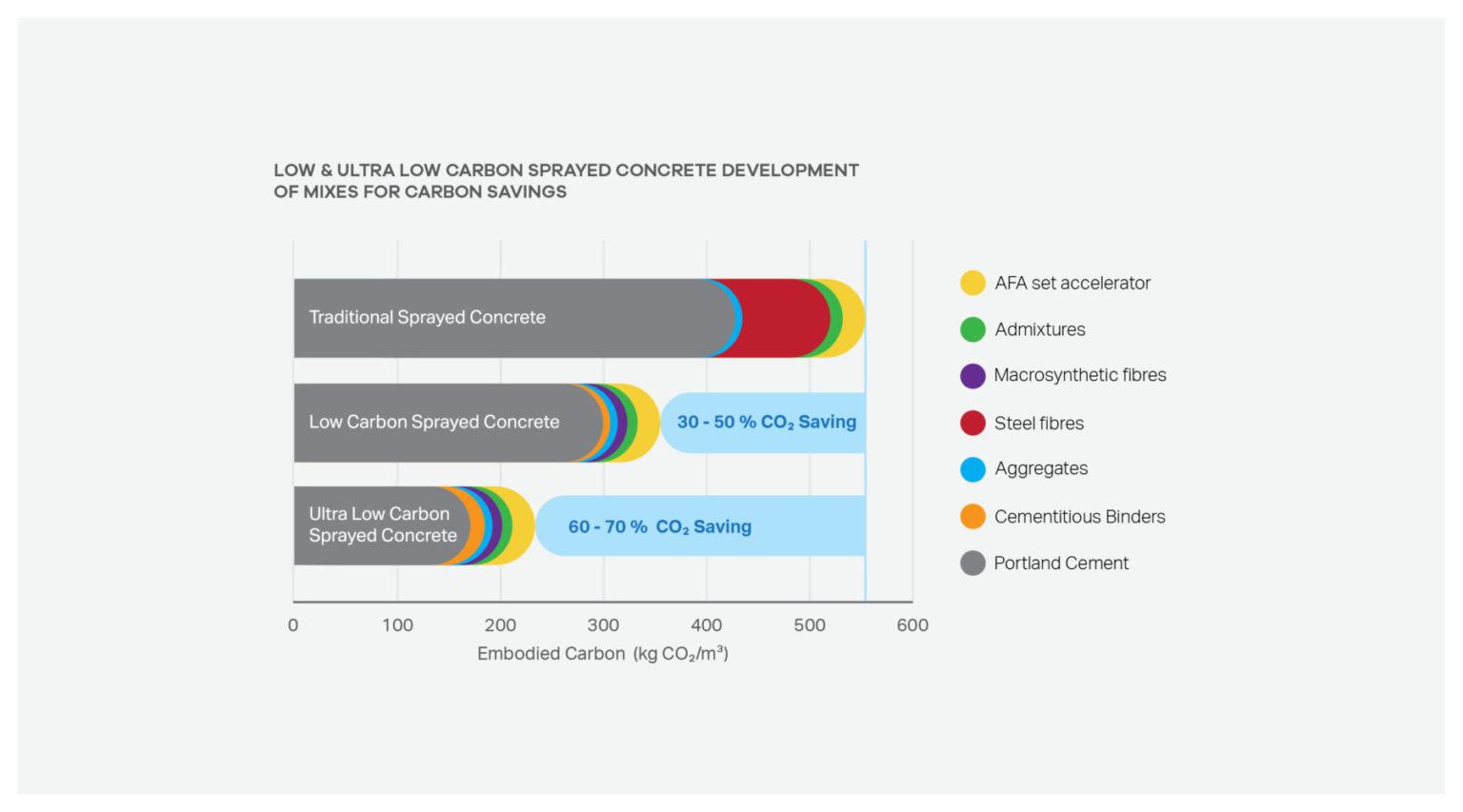
Presented in the visualisation is low and ultra-low carbon sprayed concrete development of mixes for carbon savings.
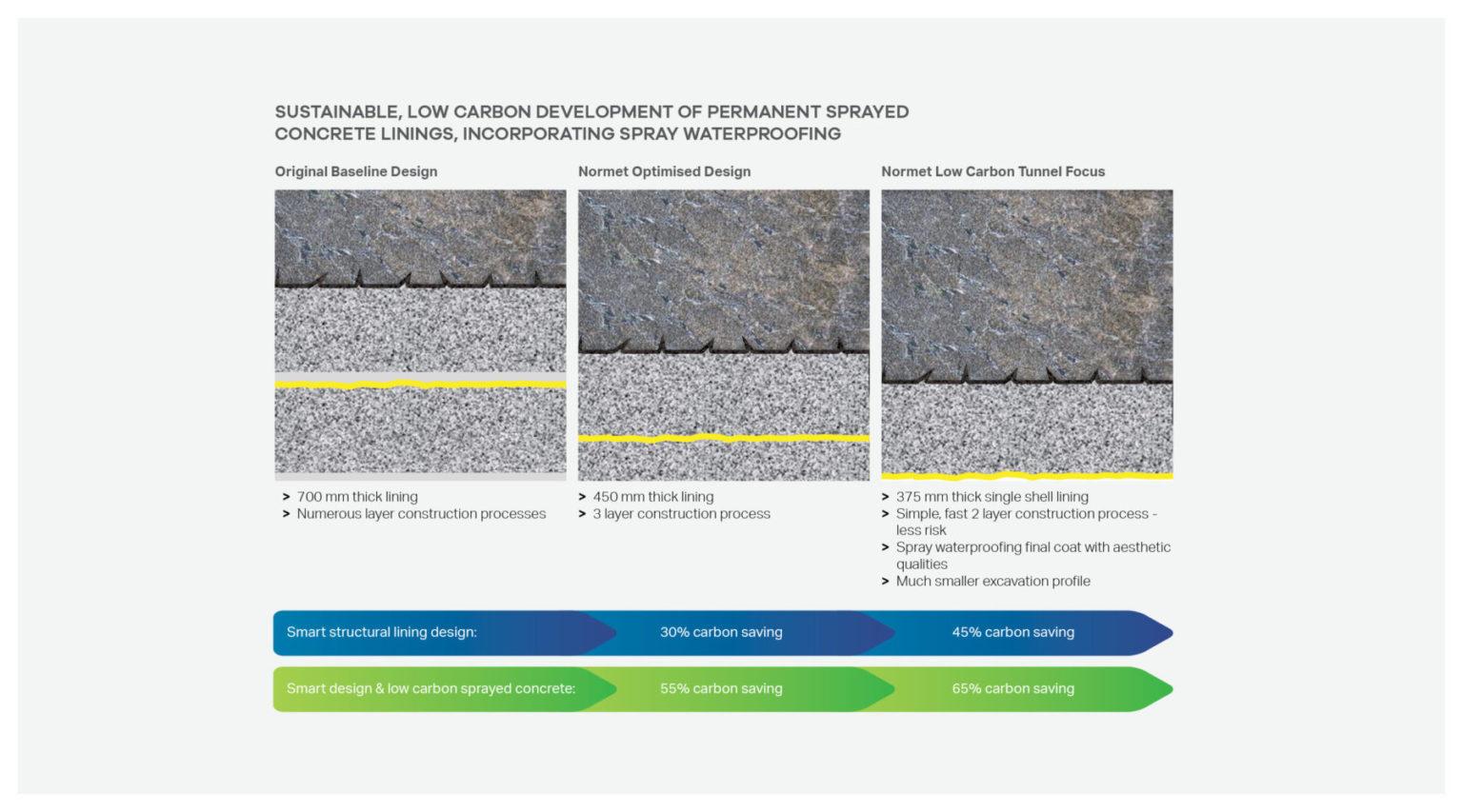
Let’s design thinner tunnel linings, specify less carbon in the concrete and reduce excavation profiles.
Normet have the edge through the ability to provide customers with a one stop shopping basket of goodies, and the expertise to support and complement them on their construction journey. In simple terms ̶ the Process offer.
Here is my take on this process. Multiple elements that all need to fit into place to function correctly and efficiently, and if they don’t, think of a 4-cylinder engine only firing on only 2 or 3 cylinders. Dysfunctional, and less than efficient at best. Need I say more?
The sprayed concrete process is one that involves elements from an equipment, service, and construction chemical perspective, not to mention the experts that piece it all together in the most efficient order. Below is what’s needed for the wheels to turn smoothly.
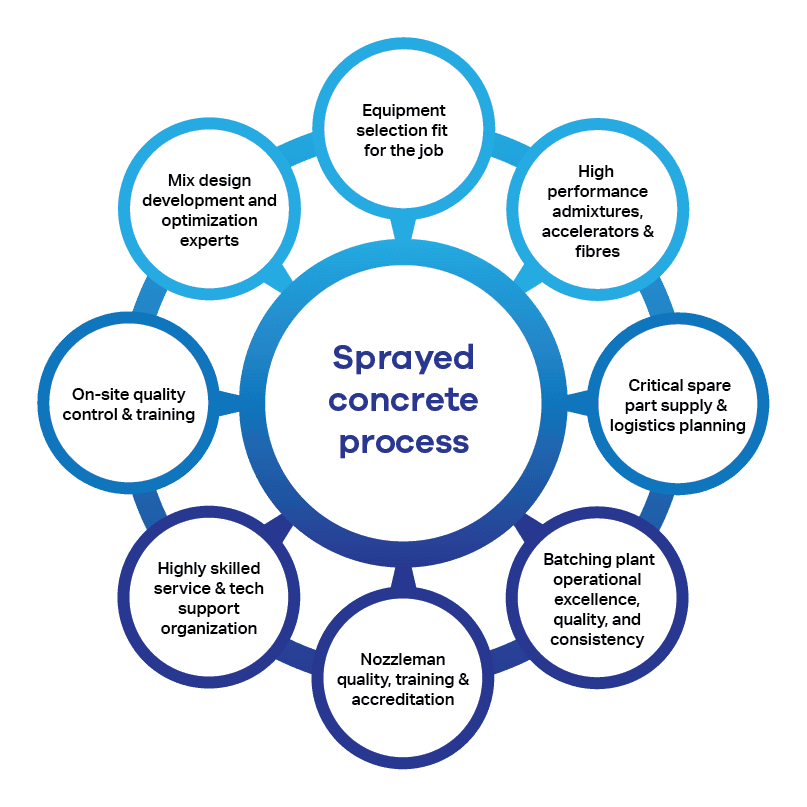
Sprayed Concrete Holistic Process
Smart people
Every element in the process is equally important. State-of-the-art equipment, services (e.g. spare parts, refurbishments, rebuilds and simulators), high-quality chemicals and very astute, knowledgeable, hands-on people. Niche professionals in their field, who can ultimately ensure that a homogeneous combination of aggregate, sand, less and less cement, more and more low carbon binders plus other bits and pieces will fly out of the nozzle tip and stick to the wall with just the right velocity that prevents it all from bouncing back in your face, and hey presto we have process excellence.
Nozzleman training and assessment leading to EFNARC Certification for operators, digitalisation, state of the art virtual reality simulators, scanning and advanced robotic spraying technology are the new nozzleman’s vision and thickness guide. We can forget hammering nails and pieces of mesh into the rock or soil.
Our sprayed concrete process is constantly developing, with evolving digitalisation and progressive technology ultimately contributing to a cleaner, safer work environment.
About the author
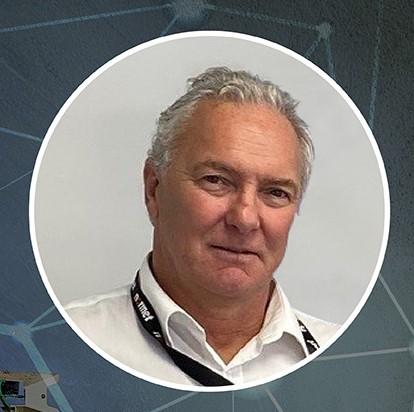
Ritchard Hood
Director, Sprayed Concrete Process at Normet
Bio
An industry professional with over 30 years of experience in tunnelling and mining, his expertise includes sprayed concrete design, application procedures, and associated equipment, chemicals and mix designs.
Ritchard Hood - LinkedIn Profile