28. Juni 2022
Unser Know-how ist unterirdisch
Wer Normet verfolgt, hat vielleicht schon bemerkt, dass wir stolz darauf sind, Experten für die unterirdischen Produktionsprozesse unserer Kunden zu sein. Indem wir dies unserem Publikum vermitteln, wollen wir zeigen, dass wir die Prozesse, für die wir Lösungen entwickeln, kennen, aber was bedeutet das für uns?
Zyklischer Prozess
Der Tunnelausbruch ist ein zyklischer Prozess, der bei so gut wie allen anderen Methoden außer der Tunnelbohrmaschine (TBM) abläuft. Auf die eine oder andere Weise folgt auf den Aushub des Materials der Abtransport aus dem Tunnelraum und die Sicherung des Profils, damit es sicher und bereit für den nächsten Aushub ist. Dies bedeutet nicht nur, dass alle Teilprozesse sorgfältig geplant und optimiert werden müssen, sondern auch, dass die Abhängigkeiten und Auswirkungen zwischen ihnen bewertet und verstanden werden müssen, um den gesamten Tunnelvortriebs- oder Abbauzyklus zu optimieren.
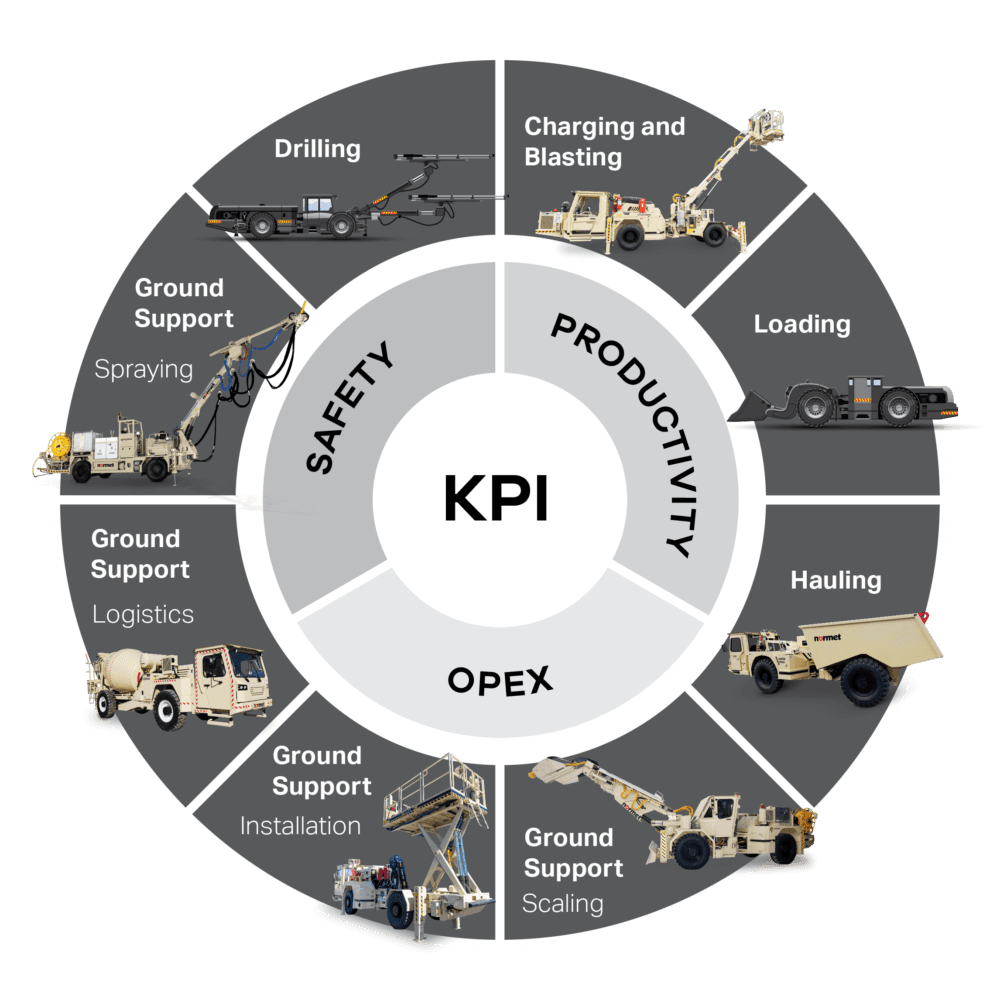
Tunnel excavation is a cyclic process where all sub-processes affect each other
Chance auf Verbesserung unter jedem Stein
Betrachten wir zum Beispiel das Bohren und Sprengen von Hartgestein und beginnen wir unsere Morgenschicht mit dem Bohren von Sprenglöchern für eine neue Runde. Es ist klar, dass der Sprengmeister diese Löcher schön und sauber an der richtigen Stelle haben möchte, damit er die Runde für optimale Sprengergebnisse aufladen kann.
Aber wie wirkt sich dies auf die folgenden Prozesse aus?
Eine sorgfältige Gestaltung des Bohrmusters und eine genaue Bohrung ermöglichen eine genaue Ladung, ohne dass zusätzlicher Sprengstoff als Ersatz für Lochabweichungen verwendet wird. Dies führt zu weniger Überbrüchen, einer glatten Oberflächenbeschaffenheit und einer engen Schadenszone.
Da die Überbrüche kleiner sind, muss weniger Gestein ausgespült werden. In Verbindung mit der kontrollierten Partikelgröße führt dies zu kürzeren und besser vorhersehbaren Aushubzeiten ohne Unterbrechungen und mit weniger Risiken.
Eine glatte Oberfläche und eine geringe Beschädigungszone haben einen großen Einfluss auf die Skalierung. Es gibt weniger loses Gestein und Unsicherheiten in der umgebenden Gesteinsmasse, und die Schuppung wird systematischer. Auch hier wird Zeit gespart, und der Zeitplan wird berechenbarer. Das Wichtigste ist jedoch, dass die Schuppung sowohl für den Bediener als auch für alle, die den Raum betreten, sicherer wird.
Eine kontrollierte Schadenszone verringert den Bedarf an Felsverankerungen und macht die Arbeit noch sicherer. Selbst wenn die Felsverankerung systematisch erfolgt, wie es in Tunneln im Tiefbau oft der Fall ist, verkürzt die glatte Oberfläche die Zeit für das Bohren der Bohrlöcher und macht die Arbeit einfacher und sicherer, da die Löcher sauber und offen bleiben.
Wie wir wissen, ist das Spritzen von Beton ein sehr materialintensiver Prozess. Ein großer Teil der Kosten für Spritzbeton entfällt auf die Betonmischung selbst, und so gut wie alle anderen Kosten hängen vom Betonverbrauch ab. Leider ist auch der derzeitige Kohlenstoff-Fußabdruck von Beton nicht gerade bewundernswert.
(Aber er kann verringert werden! Lesen Sie Ross Dimmocks (Vizepräsident, Tunnelbau) ausgezeichneten Normet-Blog: Schritte zur Schaffung von kohlenstofffreien Tunneln
Was wir oft nicht bedenken, ist, dass es unter fast jedem Felsen im Tunnel Möglichkeiten gibt, den Materialverbrauch zu senken. Eine glatte Gesteinsoberfläche mit geringen Ausbrüchen ist eine dieser Möglichkeiten. Es muss einfach weniger Fläche besprüht werden, und die Grundlagen guter Applikationstechniken, wie die Einhaltung des richtigen Abstands und Winkels zwischen Düsenspitze und Oberfläche, sind viel einfacher einzuhalten. Das Sprühen wird systematischer und die Schichtdicken bleiben besser unter Kontrolle. Dies führt unweigerlich zu einem geringeren Betonverbrauch bei gleichem Aufbau, unabhängig davon, ob die Schichtdicke oder das Profil erreicht werden soll.
Einige der anderen Möglichkeiten, den Betonverbrauch zu kontrollieren, liegen eher in den Händen von engagierten Spritzbetonspezialisten. Geschicktes und motiviertes Personal, das die Schichtdicke genau kontrolliert, eine gute Auftragstechnik, eine qualitativ hochwertige Rezeptur und eine erstklassige Ausrüstung können dafür sorgen, dass der Ausschuss auf ein Minimum reduziert wird.
Ein Teil der Arbeit ist bereits erledigt, bevor der Tunnelbau überhaupt beginnt. Kürzlich habe ich gelesen, wie bei einem Tunnelprojekt die Menge des verwendeten Spritzbetons um 20 Prozent reduziert werden konnte. Erreicht wurde dies durch die Verwendung einer Hochleistungsbetonmischung und die Möglichkeit, dünnere Schichten für die permanente Felsunterstützung zu planen.
Materialeinsparung an allen Fronten
Um es kurz zu machen: Ich würde die Bereiche, in denen der übermäßige Materialverbrauch kontrolliert werden kann, in fünf unterteilen:
- Konstruktion: nur die benötigten Schichtdicken und Strukturen vorschreiben zu können, mehr nicht.
- Aushubqualität und Profilkontrolle: So wenig wie möglich zusätzliche Fläche zum Spritzen zu lassen.
- Schichtdickenkontrolle: Minimierung des Überspritzens durch gute Applikationstechnik und moderne Technologien, die dem Bediener helfen, die richtigen Schichtdicken zu erreichen.
- Rückprall: Um das kostbare graue Zeug an die Wand und nicht auf den Boden zu bekommen, sind eine scharfe Auftragstechnik, Geräte, die eine pulsationsarme Förderung und eine genaue Dosierung des Beschleunigers ermöglichen, sowie eine sorgfältige Mischungsgestaltung erforderlich.
- Abfall und Verschütten: Die Dosieranlage und die Lieferverfahren müssen so optimiert werden, dass kein Beton verschwendet wird und alles bis zur Düse gelangt.
Wie wir hier sehen, werden nur zwei dieser fünf Bereiche tatsächlich direkt durch den Spritzbetonprozess kontrolliert. Die übrigen sind von anderen Prozessen des Tunnelbauzyklus oder sogar außerhalb davon abhängig. Nur wenn es gelingt, alle diese Bereiche zu optimieren, kann das bestmögliche Ergebnis im Hinblick auf den Materialverbrauch des Spritzbetonverfahrens erzielt werden.
Es ist ein Gesamtpaket!
Es reicht also nicht aus, einzelne Teilprozesse zu betrachten, sondern es ist auch wichtig, den gesamten Zyklus und die Abhängigkeiten zwischen den verschiedenen Teilen zu verstehen. Außerdem ist es wichtig, sich der Dinge bewusst zu sein, die nicht direkt auf dem eigenen Teller liegen. Hätte der Bohrer eine möglichst kurze Bohrzeit und eine möglichst geringe Anzahl von Bohrungen angestrebt, um Zeit zu sparen, hätten alle anderen Prozesse im Zyklus darunter gelitten.
Für uns bei Normet bedeutet dies, dass wir uns nicht auf einzelne Produkte und Prozesse konzentrieren und in Silos arbeiten können, um sie zu optimieren. Ein umfassendes Verständnis aller untertägigen Produktionsprozesse und die Kombination dieser Kenntnisse mit der Entwicklung hervorragender Lösungen für unsere Kunden sind der Schlüssel. Dadurch wird der gesamte Abbauzyklus für eine nachhaltigere Zukunft unter Tage optimiert. Aus diesem Grund stellen wir gezielt Mitarbeiter ein, die über Branchenerfahrung im Berg- und Tunnelbau verfügen, und geben dieses Know-how im gesamten Unternehmen weiter, um immer einen Schritt voraus zu sein.
Übrigens: Wenn Sie Sprayer sind, sollten Sie dem Bohrer bei der nächsten Frühschicht eine schöne heiße Tasse Kaffee anbieten. Es wird sich lohnen!
Über den Autor
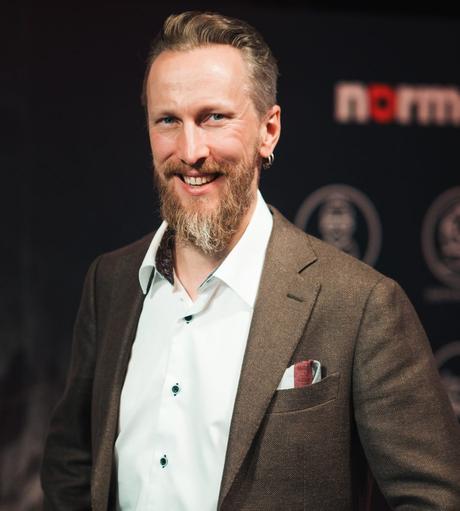
Panu Oikkonen
Director of Underground Process Excellence at Normet Group
Bio
Panu Oikkonen has been working for the underground tunnelling and mining industries for some 17 years. He has gained his on-site experience in hard rock drill & blast tunnelling projects, in positions ranging from assistant blaster to site management. Panu has a M.Sc. (Technology) degree in Rock Engineering. At Normet, Panu is developing know-how and technologies to improve underground processes. Panu is also the acting President in the Finnish Tunnelling Association FTA.
Panu Oikkonen - LinkedIn Profil